What is Postforming?
What is Postforming?
The term ‘postforming’ is used to describe the bending process applied to specially developed grades of laminate which whilst possessing all the well-known properties of standard grade high pressure laminates can also be formed into simple cylindrical concave or convex curves.
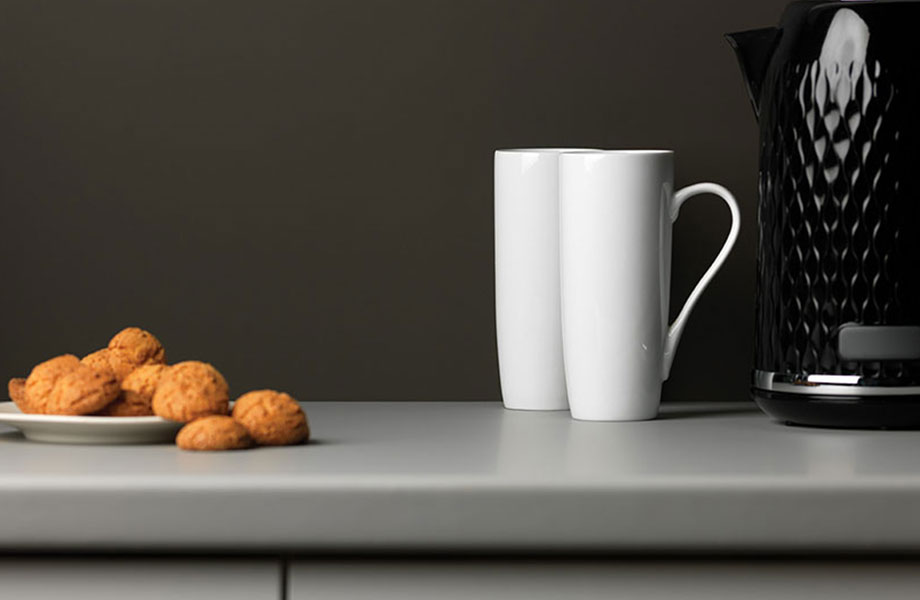
Curved surfaces with their absence of visible seams are often more aesthetically pleasing than sharp edges on internal and external angles, and will eliminate joints in which dirt and water can accumulate.
Thickness plays an important part in formability. In general, thin laminates are capable of being formed to tighter radii than thicker laminates; however for a given thickness, flame retardant postforming laminates are less formable than non-FR postforming laminates.
Unlike some postforming laminates which have a shelf-life, the formability of Formica® laminates does not deteriorate during long term storage.
Postforming Process
All postforming processes require the laminate to be heated in the area in which it is to be formed, and the best (i.e. stress-free) bends are obtained when the laminate is heated to just below the temperature at which it will blister (approximately 190°C). Whilst the method of heating will vary, the forming temperature should be attained fairly rapidly.
Practically of course there must be a reasonably wide forming temperature zone (i.e. between the lowest temperature at which the laminate will form without cracking, and the highest temperature which can be safely used without the risk of blistering). The recommended forming temperature range for Formica HGP and VGP postforming laminates is 163°C to 177°C. The recommended range for flame-retardant postforming grade VFP is 170°C to 180°C. White (light coloured) laminates should always be formed at the upper end of the temperature range.
There are a number of postforming processes available, ranging from inexpensive workshop made jigs, to sophisticated machines processing panels on two edges at speeds of up to 15 metres per minute.
Whichever process is used however, the heating of the laminate must be meticulously controlled and monitored throughout the daily working period. Fluctuations in ambient temperature, heater voltage or machine speeds may upset critical heating conditions, resulting in cracking due to insufficient heat or blistering from too much heat.
The application of heat sensitive liquids or waxes to the area to be heated is a very effective way of checking the forming temperature. These liquids/waxes melt instantly at the prescribed temperature, giving an accurate visible indication when the laminate surface has reached the required temperature.
Hand-held infrared thermometers can also be used, but care must be taken to ensure that the instrument is measuring only the temperature of the laminate surface and is not influenced by surrounding sources of heat or cold.